A Comprehensive Overview to Welding Inspection: Understanding Criteria, Techniques, and Finest Practices for High Quality Assurance
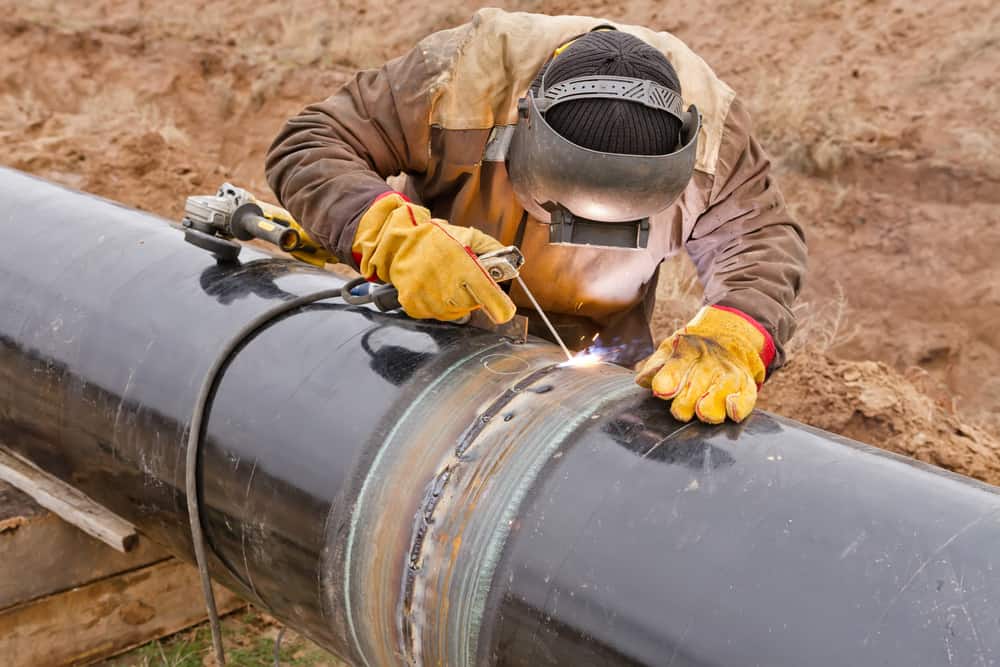
Welding examination plays a pivotal role in guaranteeing the structural integrity and safety of welded components, necessitating an extensive understanding of market requirements such as those developed by AWS and ASME. Different evaluation techniques, including ultrasonic and aesthetic screening, are utilized to find possible flaws that might jeopardize quality. Carrying out finest practices can significantly boost functional dependability and foster trust amongst customers. Welding Inspection Gilbert Arizona. As we discover these critical elements, it comes to be evident that the ramifications of welding examination expand far beyond conformity, inviting a more detailed exam of exactly how these procedures shape industry requirements and practices.
Significance of Welding Examination
Welding evaluation plays a critical role in making sure the stability and security of welded structures. It is a crucial process that confirms that welds satisfy predefined requirements, which is important in numerous sectors, including building, vehicle, and aerospace. By performing comprehensive assessments, possible defects such as fractures, insufficient blend, and porosity can be recognized early, preventing devastating failures that might cause crashes or pricey fixings.
The value of welding examination extends beyond mere compliance with regulations; it also fosters depend on with stakeholders. Customers and regulatory bodies anticipate guarantee that the frameworks they count on are constructed to hold up against functional stress and anxieties. Efficient welding evaluation practices add to lasting toughness and performance of the structures, ultimately leading to lowered maintenance costs.
Furthermore, welding inspection advertises a society of high quality within organizations, urging adherence to finest practices and continual renovation. By integrating inspection procedures into the welding workflow, firms can improve their reputation and develop themselves as leaders in quality control. To conclude, the importance of welding inspection depends on its ability to guard lives, guarantee architectural dependability, and promote industry requirements, making it a vital aspect of welding procedures.
Secret Industry Requirements
Guaranteeing conformity with essential industry requirements is vital for preserving the top quality and security of bonded structures. Different companies establish these requirements to promote finest practices in welding and assessment. Amongst the most acknowledged are the American Welding Culture (AWS) and the American Society of Mechanical Engineers (ASME), which give detailed standards and specifications for welding procedures and inspection criteria.
AWS standards, such as AWS D1.1 for architectural welding, rundown requirements for products, layout, and screening to guarantee the stability of welds. In a similar way, ASME codes, consisting of ASME Section IX, regulate the certification of welders and welding procedures, making sure regular quality in industrial applications. Worldwide, the ISO 3834 standard emphasizes quality demands for combination welding, supplying a structure for companies to show conformity with international best practices.
Conformity with these criteria not just boosts the integrity of bonded frameworks yet additionally mitigates risks associated with architectural failings. In addition, adherence to sector criteria is usually a requirement for governing approvals and can substantially influence project specifications. Inevitably, understanding and carrying out these crucial requirements are important for effective welding inspection and quality control.
Inspection Techniques Summary
Effective welding examination counts on a variety of strategies created to evaluate the top quality and stability of welds. These methods can be extensively categorized into harmful and non-destructive screening (NDT) techniques. Non-destructive testing strategies, which are widely favored in the market, permit the assessment of welds without endangering the stability of the product.
Among one of the most typically made use of NDT methods are aesthetic evaluation, ultrasonic screening, radiographic screening, and magnetic fragment testing. Aesthetic evaluation is often the primary step in the examination procedure, enabling examiners to recognize surface flaws and analyze weld bead accounts. Ultrasonic screening employs high-frequency audio waves to detect inner defects and gauge the density of welds. Radiographic screening includes making use of X-ray or gamma-ray imaging to disclose inner problems, while magnetic fragment screening is efficient for finding surface and near-surface interruptions in ferromagnetic materials.
Each strategy has its very own benefits and constraints, making it essential for inspectors to select the most suitable method based on the particular demands of the task, the materials entailed, and the urgency of the welds being evaluated. This mindful option promotes and makes certain detailed evaluations security and high quality standards in welding operations.
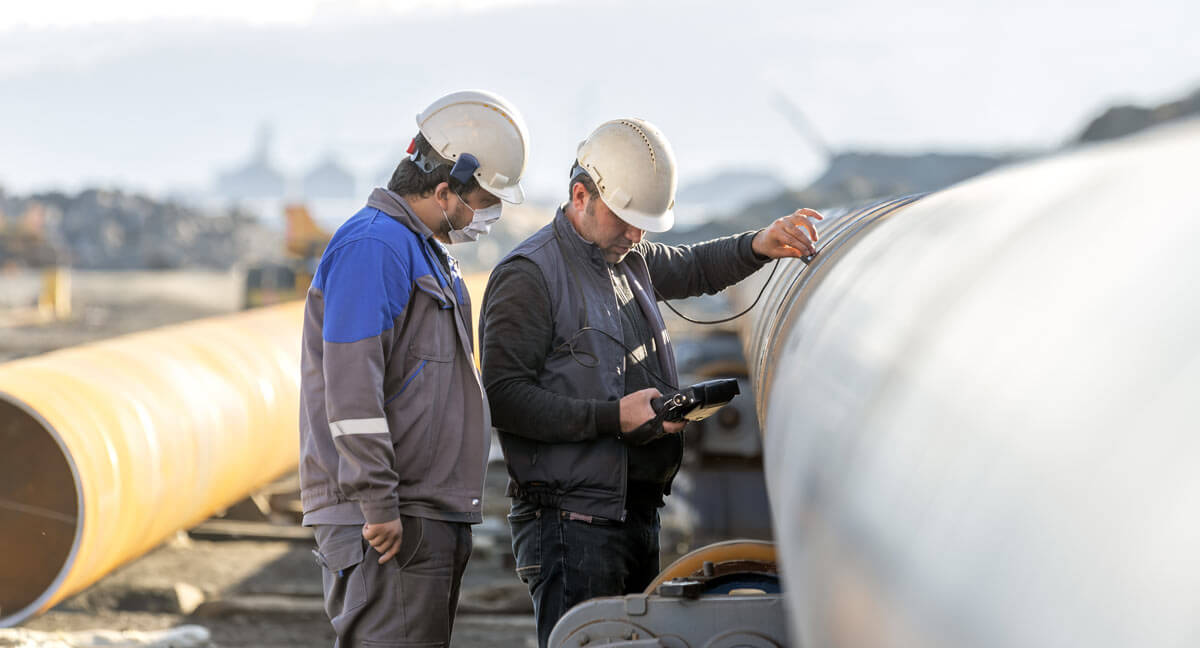
Usual Issues and Their Effects
A comprehensive understanding of typical defects in welds is essential for keeping architectural stability and security in welded constructions. Welding defects can dramatically endanger the mechanical residential or commercial properties of the joint, leading to failings that can threaten both workers and equipment.
Usual flaws include porosity, which manifests as tiny gas pockets entraped in the weld metal, weakening the total framework. Breaking is another widespread problem, frequently arising from fast cooling or improper joint layout, causing tension focus that can lead to devastating failings. Incomplete blend happens when the weld steel stops working to properly bond with the base product, creating powerlessness that may bring about separation under lots.
Various other remarkable problems consist of undercutting, where the weld bead wears down the base steel, and slag inclusions, which can impede the weld's toughness. Each of these problems has certain implications; for instance, porosity can minimize ductility, while cracking directly impacts tensile strength. Recognizing and recognizing these problems during examination is essential for making sure and applying rehabilitative measures conformity with sector standards, ultimately protecting the structural stability of bonded settings up.
Ideal Practices for Top Quality Guarantee
Applying best practices for quality guarantee in welding processes is essential for achieving optimal outcomes and minimizing problems. One vital technique is the establishment of clear welding procedures that comply with market standards and specifications. These procedures should include thorough guidelines pertaining to product option, joint prep work, and welding techniques to ensure uniformity and high quality.
Normal training and qualification of welding employees are likewise crucial. Knowledgeable welders that comprehend the relevance of top quality guarantee are most likely to produce audio welds. Furthermore, executing a durable inspection program, consisting of both non-destructive and visual screening (NDT), can assist identify defects early in the procedure, enabling for timely rehabilitative activities.
Documentation plays a vital function in quality guarantee. Maintaining exact records of view welding parameters, fixings, try this site and assessments ensures traceability and responsibility. Employing sophisticated modern technologies such as automated welding devices can improve accuracy and decrease the capacity for human mistake.
Lastly, fostering a society of quality within the company urges employees to prioritize high quality in their job. By sticking to these best methods, companies can boost the honesty of their welding processes, ultimately bring about improved product high quality and lowered costs associated with rework and repair work.
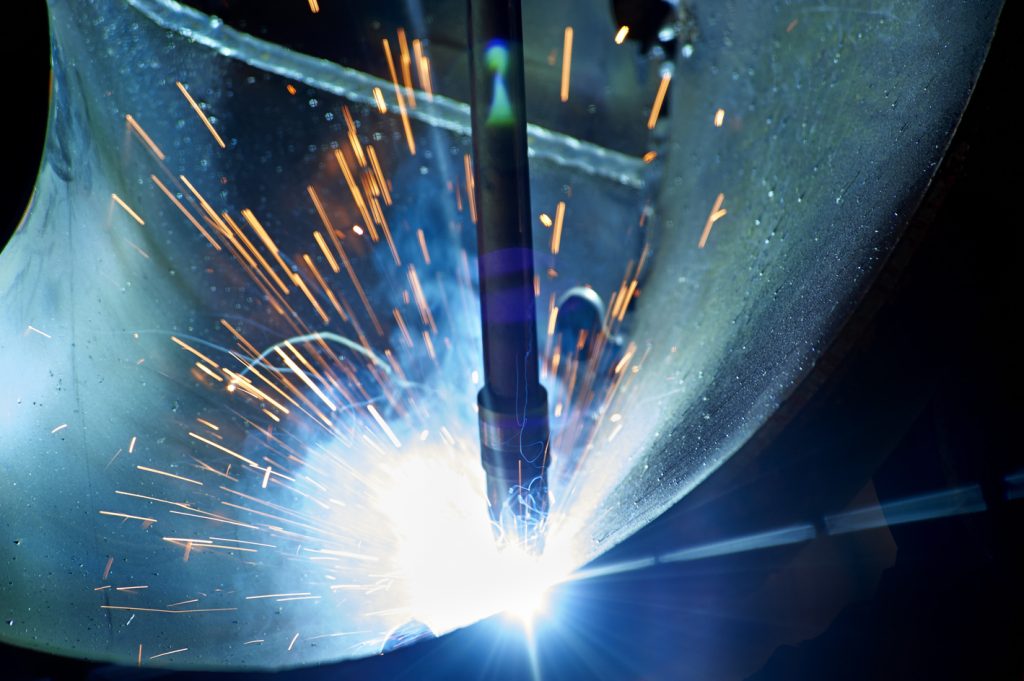
Verdict
To conclude, welding assessment plays an essential duty in guaranteeing the stability and safety and security of bonded frameworks. Adherence to key industry requirements, such as those established by AWS and ASME, is necessary for reliable quality control. Employing various inspection strategies enables the identification of common defects, thus reducing prospective dangers. By executing finest methods, organizations can enhance reliability, reduce maintenance costs, and grow trust fund amongst customers, inevitably adding to effective welding operations.
Furthermore, welding evaluation promotes a society of high quality within organizations, urging adherence to finest methods and continuous renovation. In final thought, the importance of welding inspection exists in its ability to guard lives, make sure structural integrity, and maintain industry criteria, making it a crucial element of welding operations.
Amongst the most recognized are the American Welding Society (AWS) and the American Culture of Mechanical Engineers (ASME), which give comprehensive standards and specifications for welding procedures and inspection requirements.
Inevitably, understanding and executing these vital standards are crucial for effective welding assessment and quality assurance.
Efficient welding inspection relies on a range of strategies designed to assess the high quality and honesty Click This Link of welds. - Welding Inspection Gilbert Arizona
Comments on “Navigating Welding Inspection Gilbert Arizona: Important Insights for Industry Professionals”